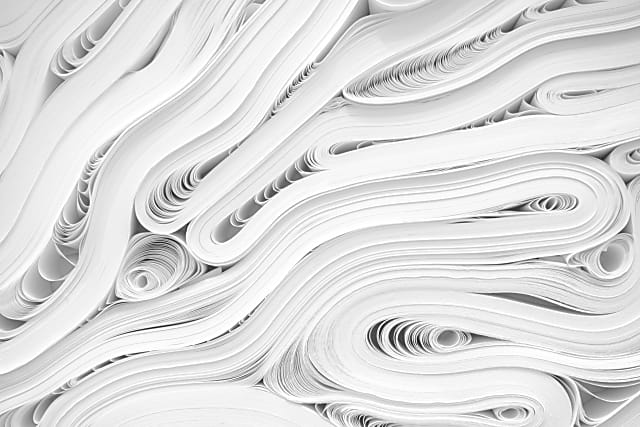
White papers
Stay up to date on the latest topics and gain industry insights from HMS' experts through our white papers, providing valuable knowledge and analysis.
In modern automotive e-production lines, efficient battery management systems (BMS) are crucial. Ador Digatron uses HMS solutions to integrate multiple BMS via a central EMS, ensuring efficient data monitoring and communication.
In modern e-production lines in the automotive industry, reliable and efficient battery management systems (BMS) are essential. Extensive data about the capacity of battery cells, charge cycles, health states, or thermal management have to be continuously read out or monitored by central control instances in battery management systems. The communication between the individual battery cells (BMS) and the higher-level energy management system (EMS) must remain efficient, scalable, and yet individual. The Indian battery manufacturer Ador Digatron relies on an HMS solution here for simultaneous integration of several BMS via a central EMS. In this way, the data from every individual battery can be simultaneously recorded and evaluated in an EMS.
The integration of several battery packs with identical communication protocols in a single master system posed a major challenge for the Indian-German joint venture Ador Digatron. Each battery pack (BMS) has thus far used the same extended identifier (29 bit) and could therefore not be differentiated by the EMS. Using extended identifiers allows more complex network structures with more participants and more unique IDs to be mapped. New devices can then be more easily integrated into existing networks without having to assign new IDs – the scalability increases.
Every BMS requires CAN messages with unique identifiers in order to ensure it functions correctly. This could not be implemented in the customer’s production environment. The previous method of generating individual requests for each battery pack was inefficient and led to considerable delays in the production process. So they were looking for a tool that could be used to reroute the CAN identifiers, i.e. individually define them, and to set the baud rates. In addition, it was to be possible to use as many CAN channels as possible at the same time.
To solve this problem, the CANbridge NT420 from HMS Networks was implemented. This intelligent CAN-to-CAN bridge allows the connection and communication between different CAN and CAN-FD networks, even if these use different baud rates and frame formats. The device offers enhanced functions, such as filtering, identifier changes, and data mapping.
Three BMS are connected per bridge via the four independent CAN channels. The fourth channel of every bridge is needed as a connection to the downstream embedded controller in the control cabinet. Several bridges together deliver the collected CAN data to this controller, which transfers via TCP/IP the CAN signal to the Ethernet required in the EMS.
In addition to the identifier change, Ador Digatron also benefits from the integrated galvanic isolation. Battery systems are often exposed to high voltages, which can damage other components in the network and lead to machine downtimes. Every CANbridge is fused up to 1,000 V, stabilizes communication, and protects all other system participants.
The software integration of the battery management system (BMS) occurs via several programs in order to ensure a seamless and efficient communication between the different components. One of the main tools was the CAN-Gateway Configurator from HMS. This Windows-based configuration tool allows for the simple configuration of the bridges via USB. It plays a key role in adjusting and translating the CAN commands for every single battery unit.
Another key tool is Cangui, a graphical user interface for creating CAN tasks. The Cangui tool generates Pascal files, which are integrated into the EMS program. These files allow the received CAN messages to be parsed and converted into EMS variables, which can be used in the entire test program. This ensures a precise and consistent data processing within the system.
The BUSMASTER tool is used to simulate and analyze the CAN communication. This open-source software is used to monitor, analyze, and simulate CAN messages and was used as a virtual BMS in this project. The BUSMASTER tool makes it possible to thoroughly check and validate the communication protocols before the actual hardware is implemented.
By using these specialized software tools, it was possible to successfully integrate the different BMS components. The careful configuration and simulation ensured a smooth and reliable data transmission, which led to an improved system performance and reliability of the Ador Digatron systems.
Company: Ador Digatron
Solution: BMS integration via CAN network gateway
Industry: Battery manufacturing
Product: Ixxat CANbridge NT420
Stay up to date on the latest topics and gain industry insights from HMS' experts through our white papers, providing valuable knowledge and analysis.
Our products solve everyday industrial communication problems. Discover how our customers have improved their business with HMS case studies.
HMS communication solutions help thousands of companies solve specific communication problems in many different industries and applications.