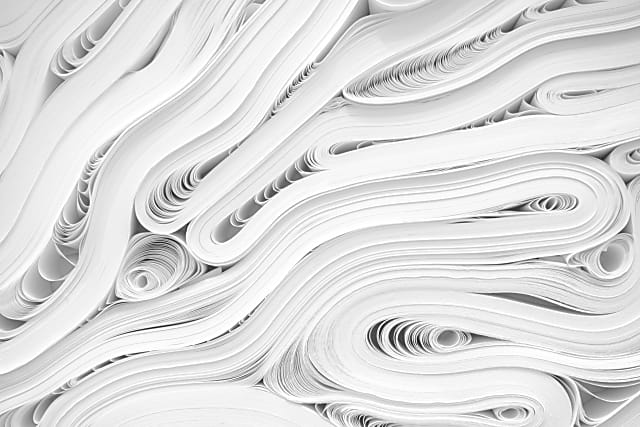
White papers
Stay up to date on the latest topics and gain industry insights from HMS' experts through our white papers, providing valuable knowledge and analysis.
To address issues such as the interference in CAN bus communication within the tower of a wind power system, a reliable CAN gateway is utilized to ensure stable communication in wind power testing.
China General Certification Center (abbreviated as CGC) is a third-party technical service organization specializing in standard development, testing, inspection, certification, technology consulting, and industry research services.
Our services span a range of industries, including renewable energy, climate change and sustainable development, industrial equipment and intelligent manufacturing, rail transit, consumer goods, intelligent technology, information security and others. CGC has a significant impact on industries such as wind energy, solar energy, and rail transit. Its testing, inspection, and certification results have been widely recognized and accepted by governments, financial institutions, and end users.
A significant communication challenge faced by wind turbine manufacturers and O&M companies is the remote and complex nature of wind turbine locations, and the extremely complicated electromagnetic environments inside the tower: various electromagnetic interference from high-power equipment such as generators and frequency converters. These can seriously interfere the collected data during transmission, resulting in communication interruptions or inaccurate data acquisition.
The current solution utilizes CAN and fiber for signal transmission to ensure stable communication. However, as the amount of data required for wind and solar power testing, the number of sensors, and the CAN bus communication distance increase, numerous issues have emerged during overall system testing. These include unstable communication, high communication delay, difficulty in communication debugging and communication failure detection.
CAN bus communication has always been a challenge in our testing and certification work for wind turbine manufacturers. In our existing solutions, we have long relied on HMS’s Ixxat CAN-CR210 for photoelectric isolation and interference shielding. However, as more powerful wind turbine towers enter centralized testing and verification, the number of data points and the amount of data we need to deal with have greatly increased. In order to meet the requirements of testing and certification in the next stage, we are seeking new products. This introduces the CAN@net NT420 gateway and Anybus managed switch, which we intend to utilize in the construction of a new communication system.
Mr. Li Shengkun, China General Certification Center
At present, we utilize the CAN@net NT 420 bridge to combine CAN bus communication with Ethernet, thereby creating 4 independent CAN bridges, each with 4 independent CAN channels. These bridges enable the exchange of CAN data between different CAN networks over long distance through TCP/IP, while utilizing existing Ethernet-based infrastructure, without additional usage costs. By dividing the CAN system into network segments, we can enhance the reliability and fail-safety of the entire system, while also streamlining troubleshooting and maintenance of specific network segments during testing.
We connect all CAN devices to the managed switch AWB5005. The two SFP (small form-factor pluggable) slots of the switch enable high-speed uplink to backbone switches and ring-configured networks within the tower. In addition, a fiber connection can be used to enable long-distance connections or to provide reliable data communication in environments with high electromagnetic interference. The network management functions include data segmentation and control, which are employed to ensure that data processing meets the expected requirements.
Mr. Li concluded that the solution combines the CAN@net NT420 and Anybus Managed L2 PoE Switch, ensuring communication stability within the wind turbine tower. In this system, the load data acquisition device transmits the collected data from the slip ring to the acquisition device at the top of the tower, which then forwards the data to the acquisition device in the tower. Finally, the data is uniformly transmitted to the data recorder and industrial server at the bottom of the tower for engineers to process the data.
During this process, the Ixxat CAN@net NT420 converts CAN signals into TCP/IP protocols, which are then transmitted at gigabit speeds through optical fibers. A communication system is then constructed to meet the requirements of wind power testing, ensuring the reliability and stability of CAN bus communication within the tower. We hope that this solution will be implemented in the testing environments of more system manufacturers.
Country: China
Solution: Network gateways
Industries: Wind power
Products: Ixxat CAN@net NT 420 and Anybus Managed L2 PoE Switch
Stay up to date on the latest topics and gain industry insights from HMS' experts through our white papers, providing valuable knowledge and analysis.
Our products solve everyday industrial communication problems. Discover how our customers have improved their business with HMS case studies.
HMS communication solutions help thousands of companies solve specific communication problems in many different industries and applications.