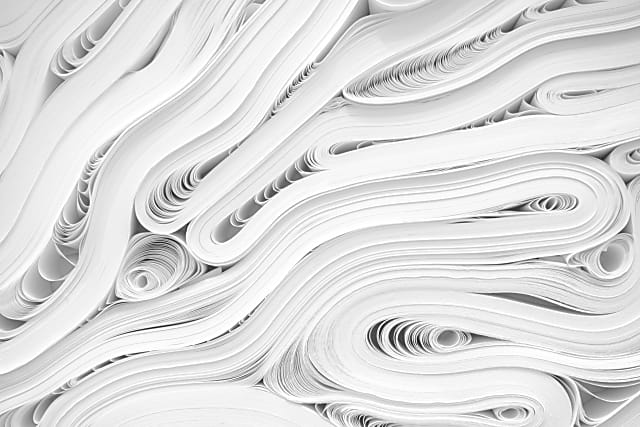
White papers
Stay up to date on the latest topics and gain industry insights from HMS' experts through our white papers, providing valuable knowledge and analysis.
UK Power Networks Services used the Ewon Cosy to provide remote access for power quality monitoring at a critical UK water treatment plant. The Ewon Cosy cellular gateway established a secure VPN connection, enabling engineers and operators to access data from power quality monitors remotely.
UK Power Networks Services needed to deploy power quality monitoring at a major UK water treatment plant. Part of the contract included remote access to operational data to streamline the process. The Ewon Cosy proved to be the ideal choice.
National water supplies are classified as critical infrastructure in the UK and many other countries. In this respect, they attract more attention when they go wrong and must place concerted emphasis on maintaining 100% up-time.
The water industry relies heavily on other critical utilities, including electricity. So, in much the same way, the electrical suppliers have to be just as committed to helping their water-industry customers maintain as close to 100% up-time as possible.
A typical water treatment plant will consume a lot of power across multiple disciplines and services, and keeping tabs on all this supply and consumption is a full-time job. Power quality levels and uninterrupted supplies are extremely important.
In a recent application, UK Power Networks was approached by a major UK water supplier who was experiencing power quality issues at a large treatment works. They were tasked with identifying causes of disruptions that could not be directly attributed to a simple power outage of the incoming electricity supply. These disruptions can be caused by momentary dips in the electricity supply voltage levels. Although they may only be for a fraction of a second (<100 ms), they are often sufficient for motor controls or local control systems to crash.
The Ewon Cosy securely connects us in the office to the meters in the remote location. We are then able to review the records in the power meter, review the event list and see if there are any disturbances.
Rinu Ravikumar, Senior Design Engineer, UK Power Networks
The scope of work included the supply of three Siemens SICAM Q100 voltage and current quality devices on each of the incomers, which will provide permanent power quality monitoring of the feed-in locations. Another essential element of the installation was a communication solution that would allow engineers and operators to access the data from these devices remotely. For this role, UK Power Networks turned to HMS Networks and its Ewon Cosy cellular gateway, an industrial device that establishes a secure VPN connection between the power quality monitors and the operators, no matter where they are. The connection is made through Talk2m, a highly secured industrial cloud service included for free with the gateway.
According to Rinu Ravikumar, Senior Design Engineer at UK Power Networks: “The power quality meters record disturbances or deviation from the expected power quality levels. The Ewon Cosy securely connects us in the office to these meters in the remote location. We are then able to review the records in the power meter, review the event list and see if there are any disturbances. Moreover, we can also extract historic disturbance records from these power meters and then analyse the electrical characteristics of the network to provide recommendations to improve power quality. From this we can generate a report that captures all this information, ultimately helping to improve power resilience to the customer. We utilise the Ecatcher application to access these meters from our engineering laptops,” he adds, “while our customer or local engineer uses M2web to access the meters remotely using the internet.”
The benefits of this remote connectivity solution include:
Bilal Khan, Technical Sales Manager at HMS Networks, concludes: “The remote access capabilities offered by the Ewon Cosy saves both UK Power Networks and its water industry customer significant amounts of time and effort and with the data analysis. Further gains should be achievable in the future as more proactivity kicks in. One of the primary goals was to allow the engineers to work more efficiently, which this installation certainly achieves. Even if the engineers have to go on-site, the rich data made available means they don’t need to hunt for issues, as they can now locate causes much more quickly.”
Stay up to date on the latest topics and gain industry insights from HMS' experts through our white papers, providing valuable knowledge and analysis.
Our products solve everyday industrial communication problems. Discover how our customers have improved their business with HMS case studies.
HMS communication solutions help thousands of companies solve specific communication problems in many different industries and applications.