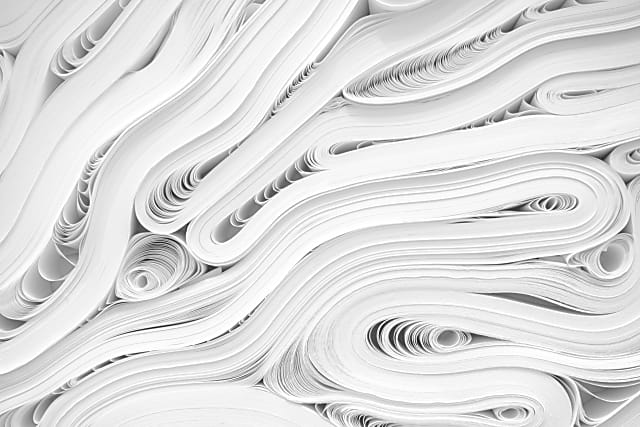
White papers
Stay up to date on the latest topics and gain industry insights from HMS' experts through our white papers, providing valuable knowledge and analysis.
Fast roaming and seamless data communications, enabled by Anybus. Wireless networking technology is ensuring the reliable operation of automated guided vehicles (AGVs) for a Swedish manufacturer of heavy vehicle components - helping increase their production efficiency and throughput.
The manufacturer tasked Swedish Löfqvist Engineering AB with designing and implementing a new automated solution for its large production area. Löfqvist Engineering is an industrial automation and robotics company that supports manufacturers by implementing solutions to eliminate manual and heavy lifting processes within production lines and on factory floors.
The solution involves the manufacturer’s existing machine centers – which performs all production functions such as turning, reaming and hardening. This is now being replaced by eight automated, function-specific production cells which produce the various vehicle components.
Critical to the project was the integration of these production cells, and the efficient movement of components between the cells, and in and out of the production facility.
This labor-intensive task had previously been performed manually, which involved a lot of heavy lifting and was inefficient. The manufacturer initially considered fixed conveyor belts, but concluded that AGVs would be a more productive solution that would also provide greater flexibility when adapting to changing production demands.
Löfqvist Engineering developed and implemented three AGVs to move specific components to the appropriate production cells, while a fourth was fitted with a highly flexible mobile collaborative robot (cobot) to perform quality checks on the parts. Because the AGVs move freely between the production cells to supply and collect components as required, reliable wireless communication is essential.
David Lundgren from Löfqvist Engineering was responsible for getting the system up and running in the factory. Implementing a wireless network in this type of industrial environment requires knowledge and planning, something that HMS Networks can also provide as part of their service offering if needed.
Löfqvist Engineering has a long and trusted relationship with HMS Networks, and opted to implement an Anybus wireless communication solution for this new production system. Anybus technology is widely applied throughout the automotive industry to enable devices, machines and robots to communicate wirelessly with a factory’s industrial network.
HMS Networks engineers supported Löfqvist Engineering in implementing the solution, which included mounting two Anybus Wireless Bolt™ devices on each of the AGVs to enable connection to a wireless network via Bluetooth or Wireless LAN.
Designed to perform reliably in the harsh environments in factory automation, a Wireless Bolt is a compact, all-in-one package that features a connector, communication processor, and integrated antenna in the same unit, with IP67-class protection. Because of the limited space available on the AGVs, this compact form factor was critical.
One Wireless Bolt is connected to an onboard Omron PLC (that manages the AGV’s movement and safety functions) and provides communication with a central supervisory PLC system.
The second Wireless Bolt is connected to the AGV’s robot controller and provides wireless access to remotely configure or troubleshoot the AGVs via a browser on a handheld device such as a tablet, laptop or smartphone. This eliminates the need for an external HMI mounted on the cobot, which provides flexibility and mobility, saves costs by eliminating the need for an HMI, and means that a machine operator or technician does not need to be physically located at the machine to gain access, thereby increasing personnel safety.
Because the manufacturer’s overall production area is so large, the solution required three Anybus Wireless Access Points (APs). These industrial-grade infrastructure hubs are installed at strategic points to form the wireless network and ensure an overlapping coverage area that facilitates roaming.
The Anybus products support the IEEE 802.11r standard for fast roaming (also known as fast BSS transition) within a wireless network. This is extremely useful for applications involving AGVs, where seamless connectivity is required across the entire factory floor to ensure that the AGVs are always in contact with the network.
Wireless roaming is when a client device moves around in an area with multiple APs and may automatically switch from one AP to another that has a stronger signal. Without fast roaming support, that transition would require the client to re-authenticate. As a result, there could be a delay and loss of connection, which could trip an emergency stop, thereby impacting production efficiency.
However, with fast roaming, client devices are authenticated to the first AP and their credentials are forwarded to the next AP prior to roaming, which eliminates the need for re-authentication. This significantly reduces the handover time, while still maintaining network security.
The Anybus Wireless access points, with Mesh capabilities, provide excellent network coverage and seamless roaming throughout the production area.
The supporting wireless network infrastructure uses an Anybus X-gateway to provide seamless communications between the onboard and supervisory PLCs. Because the AGVs employ automation technology from different vendors, this created a situation where different data communication protocols were used.
For example, the Omron PLC that uses EtherNet/IP communications over the wireless network needs to connect to a Siemens supervisory system that uses Profinet communications. The easy-to-use Anybus X-gateway simplifies this multi-vendor PLC solution by translating between EtherNet/IP and Profinet.
Successful Installation
The AGVs are operating almost continuously - 24 hours a day, which has enabled the manufacturer to increase production to 5000 units a week, with spare capacity available to support future growth.
As well as increasing throughput, the manufacturer is also ensuring quality. The reliable and resilient HMS Networks Anybus communication solution is playing a pivotal role in achieving these results by ensuring seamless data network connectivity across the entire factory floor.
AGVs usually come with built-in wireless connectivity for regular operation, e.g. for assigning new tasks and routes. When mounting additional equipment onto the AGV, like a robot arm in this case, this equipment may need a separate wireless connection. The Anybus Wireless Bolt, with its unique form factor, is perfect for this application. The IP and MAC address of the equipment can be cloned and exposed to the wireless network in a way so that the Anybus Wireless Bolt is completely transparent.
Company: Löfqvist Engineering AB
Country: Sweden
Solution: Wireless Infrastructure
Industries: Robotics
Products: Anybus Wireless Bolt
Stay up to date on the latest topics and gain industry insights from HMS' experts through our white papers, providing valuable knowledge and analysis.
Our products solve everyday industrial communication problems. Discover how our customers have improved their business with HMS case studies.
HMS communication solutions help thousands of companies solve specific communication problems in many different industries and applications.