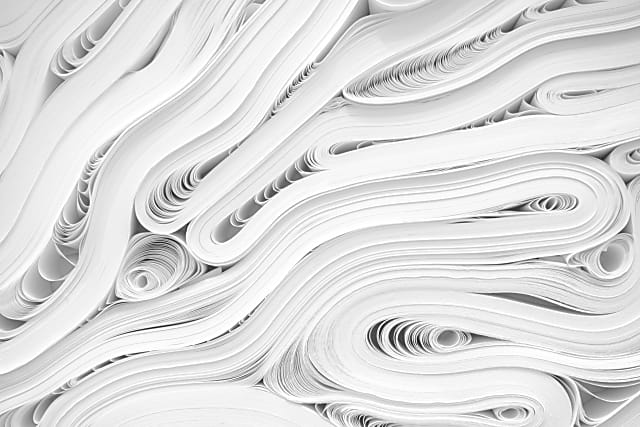
White papers
Stay up to date on the latest topics and gain industry insights from HMS' experts through our white papers, providing valuable knowledge and analysis.
The Ixxat CAN@net NT 200 enables easy remote access to CAN-based control systems via Ethernet. Remote monitoring helps to optimize the maintenance plan so that improper use, operating errors, deterioration, etc. can be considered accordingly.
Statistically, elevators are the safest means of mass transportation. They facilitate the movement of – not only physically restricted – persons in shopping centers, residential and office buildings, hotels and other public institutions. For safety reasons, elevators must be inspected in legally prescribed intervals*. But what about the safety between these test intervals? Particularly in the case of larger elevator systems, which are subject to intense use, continuous monitoring of the safety-relevant devices is preferable.
An alarm button and an intercom system are legally required “basic equipment” for all elevators since 1998 in Germany. In modern elevator systems, however, a large number of sensors are installed additionally which provide information on all types of data about the elevator. These sensors record acceleration, speed, driving quality and more. All these values are reported to the decentralized elevator control.
While the communication between the sensors and the elevator control often is done via CAN bus technology, the transmission of the data from the elevator control to the centrally located monitoring center is not possible via CAN due to the physical limitations. For this purpose, Ethernet is the medium of choice.
To convert the CAN protocol to Ethernet and thereby read, display and centrally manage the elevator data from afar, CAN-to-Ethernet gateways are used. With one “leg” – the CAN interface – connected to the elevator control and the other “leg” – the Ethernet port – connected to the LAN network of the building, the gateway serves to process the sensor data for transport via Ethernet and to report the status data of the elevator to a central location via Intranet/Internet.
The CAN@net NT 200 is a new solution from HMS for coupling of CAN bus technology and Ethernet networks. With one Ethernet port and two CAN interfaces as well as corresponding software, it is ideal for quick, easy and reliable data exchange with low latency between the different networks.
In the elevator monitoring application, the CAN@net 200 connects one or two CAN nodes via Ethernet to the monitoring computer in the control center (host system). For this purpose, the CAN@net NT 200 is connected to the monitoring computer in gateway mode. The computer can be equipped with any type of operating systems (Windows, Linux, VxWorks or QNX); in addition, the data exchange is also possible with embedded devices.
The communication between the monitoring computer and the CAN@net NT 200 is carried out via a standard TCP/IP socket and an easy-to-implement ASCII protocol, which facilitates the transfer of data into the monitoring or display software. Since the communication between the host and the CAN@net NT 200 is done via standard TCP/IP, existing Ethernet networks in the building can be used. This allows for easy upgrading of existing facilities by combining CAN bus technology with Ethernet as well as cost-saving and time-saving use of existing infrastructure.
Wrapping it up, it can be said that the CAN@net NT 200 – as a CAN-to-Ethernet gateway – provides easy and flexible access to CAN systems over LAN or over the Internet.
Benefits of the Ixxat CAN@net NT 200
Solution: CAN connectivity
Industries: Building automation
Products: Ixxat CAN bridges and gateways
Stay up to date on the latest topics and gain industry insights from HMS' experts through our white papers, providing valuable knowledge and analysis.
Our products solve everyday industrial communication problems. Discover how our customers have improved their business with HMS case studies.
HMS communication solutions help thousands of companies solve specific communication problems in many different industries and applications.